К реакторам высокого давления относят емкости, которые работают под давлением свыше 20 атм.
Такие реакторы применяют в производствах:
- мочевины
- присадок для биотоплива
- катализаторов
- метанола
- искусственного жидкого топлива
- различных других химических процессах
Проектирование и изготовление аппаратов высокого давления дело весьма ответственное.
Конструктивно реакторы высокого давления делятся на две группы:
- автоклавы – емкости с перемешивающим устройством и
- колонные аппараты для проведения непрерывных процессов.
В реакторе, предназначенном для работы с коррозионно-активными веществами, конструкцией предусматриваются вкладыши из кислотостойких материалов, таких как фторопласт или тантал.
Для того чтобы обеспечить герметичность и безопасность работы, реактор высокого давления снабжен фланцами из высокопрочной конструкционной стали, в которых для облегчения сборки вместо отверстий для болтов сделаны прорези, куда вставляют болты с Т - образной головкой.
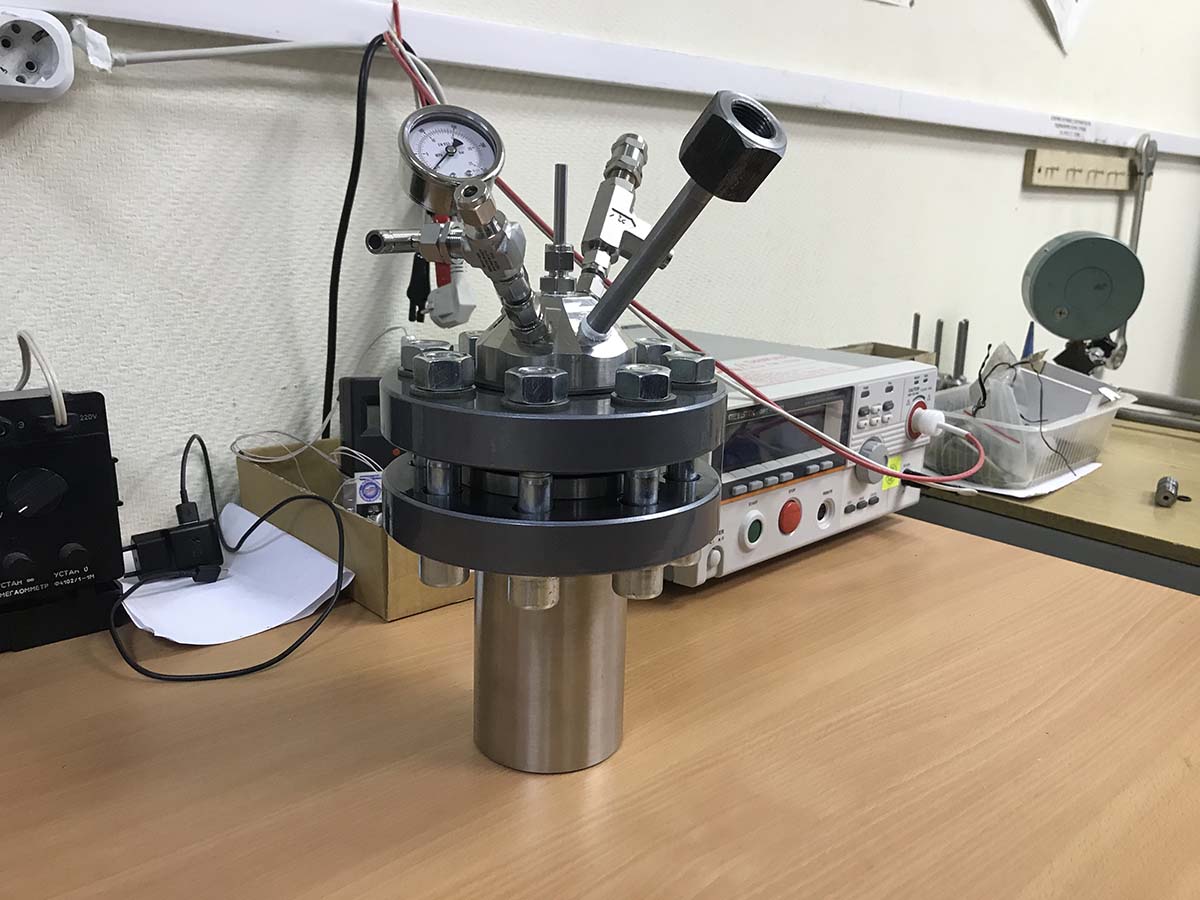
Автоклавы небольшого объема до трех – пяти литров изготовляются на токарном станке из цельной заготовки. Перед запуском в производство заготовка проходит процедуру не разрушающего акустического и радиационного контроля, которая, гарантирует отсутствие скрытых дефектов в рабочем материале.
Герметичное соединение крышки с корпусом автоклава достигается с помощью байонетного затвора или фланцевого соединения типа "шип-паз". Для затягивания болтов применяются динамометрические ключи, которые позволяют контролировать момент затяжки метизов.
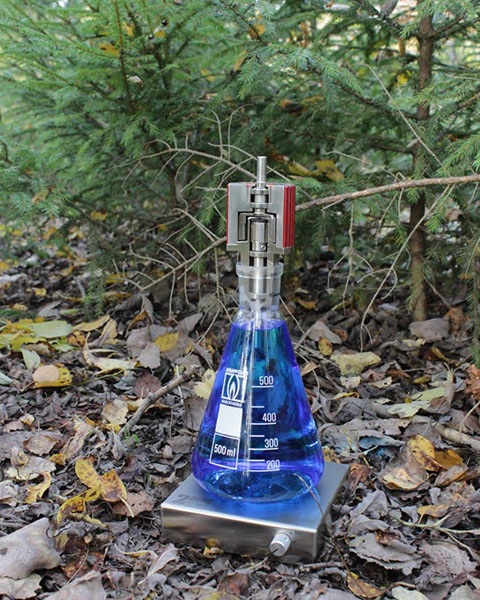
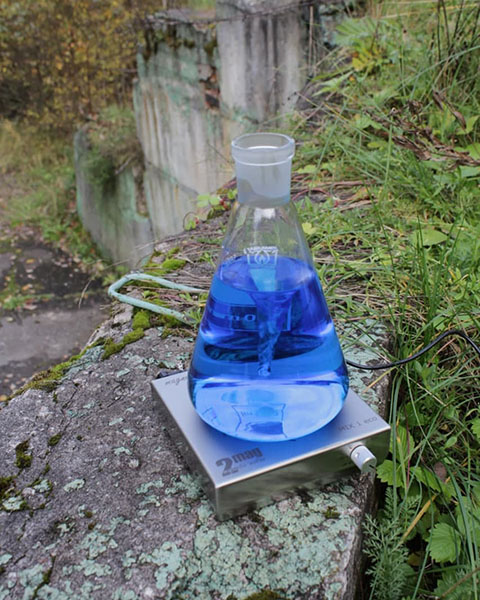
При давлениях внутри реакционной емкости более 20 Атм рекомендуется применять бессальниковый герметичный привод, оснащенный магнитной муфтой. В этом случае ротор электродвигателя крепят непосредственно на вал мешалки. Его отделяют от статора защитной гильзой и приводят в движение вращающимся магнитным полем статора.
Уплотнения реакторов высокого давления
Применяются уплотнения следующих видов:
- с мягкими металлическими прокладками прямоугольного, треугольного или овального сечений, конусные и двухконусные,
- с упругим металлическим кольцом.
В качестве прокладок используется медь, алюминий, мягкое железо, фторопласт, графит.
При соединении трубопроводов используется коническое или линзовое уплотнение.
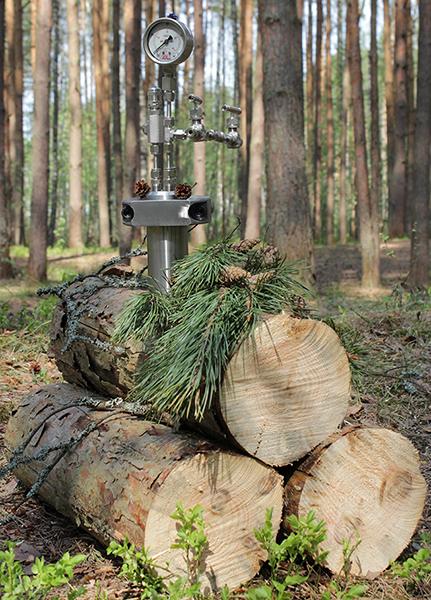
Аварийный клапан сброса давления и разрывная мембрана гарантируют безопасность работы реактора и сохранность оборудования.
При некоторых процессах требуется нагреть реактор или наоборот охладить его.
Для нагрева реактора применяют две схемы: электрическую или жидкостную во внешней рубашке.
Для охлаждения реакционной емкости используют жидкостную схему охлаждения, внешним контуром или внутри емкости через специально разработанный спиральный теплообменник.
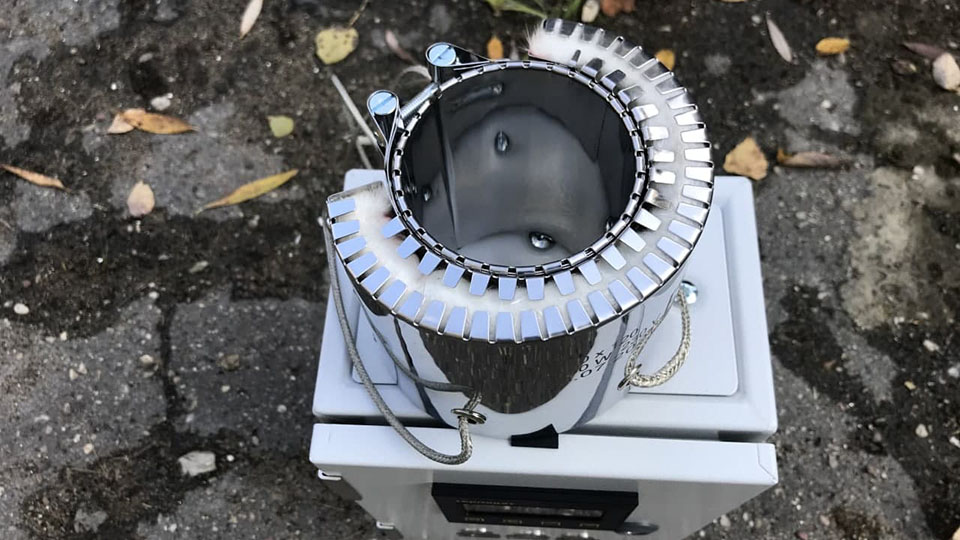
Задаваемые рабочие параметры, контроль протекающих процессов, информация о состоянии системы и продукта выводятся на внешний пост управления.
Многие операции, к примеру, дозированная подача продукта в емкость, продувка газом, термостатирование и прочее могут быть автоматизированы при помощи специально разработанного программно-аппаратного комплекса.
Для обеспечения выполнения поставленных задач предусматривается различное дополнительное оборудование, которое устанавливается на химический реактор.
Узлы отбора и возврата проб, сливные краны, термопары, датчики контроля давления, системы телеметрии и многое другое в соответствии с техническим заданием.